Heat Exchanger division
Our Activity

- Mechanical & Thermal Design Calculations
- New Manufacturing of all type Heat Exchanger & Louvers
- Re-Tubing
- Chemical Cleaning & Circulation
- Refurbishment
- Re-certification
- Survey & Inspection service
- Shutdown activities
- Onshore & Offshore Skilled Manpower supply
- Supply of fasteners, Spares & testing accessories
Turnaround Services

- Super Engineering Industry Projects Division specialized in undertaking plant turnarounds & shoutdown. We specialize in overall project planning and Engineering, Material procurement, Manpower Sourcing and Allocating, Site coordination and Execution.
- Super Engineering Industry follow a time tested exceptional Quality Management System. Our experienced inspection team carries out a thorough check up of the entire plant leaving a detailed and informative Quality Dossier on plant's health and future recommendations.
- With a talented and well-managed workforce spread across the Middle East, we are confident in taking up any type of maintenance and servicing challenge requirements from our clients. Our services are always available to our clients 24x7 within the reach. SEI has in house resources such and tube bundle extractors, Ultra High pressure water jetting units, chemical circulation skids, software supported bolt management systems makes us more reliable along with our disciplined and trained work force.
Re-Tubing

- Heat Exchangers being utilized in the Oil and Gas installations often have corrosive and viscid fluids and gases flowing through its tubes. As heat exchanger's age, their performance declines overtime, due to fouling, erosion and corrosion, thus requiring periodic refurbishment and repair. An effective and cost efficient solution is re-tubing of the exchanger.
- Super Engineering Industry has earned a reputaiton of being a specialist provider of re-tubing services. The key advantage being is that it undertakes all associated works with re-tubing such as the exchanger blinding, Tube bundle extraction, the procurement and testing of the raw materials, on-site/off-site re-tubing and finally the bundle installation and equipment commissioning.
- Super Engineering Industry is equipped with a wide range of specialized re-tubing equipment and is aided by its highly trained and experiences teams, allowing it to take any challenges and any conditions. With Super Engineering Industry you can be assured of a Quality and Timely completion of any projects.
Hydro Jetting

Super Engineering Industry provides a variable high pressure water jet system. The diesel drive high pressure unit delivers an operating pressure up to 40,000 PSI. Our Hydro jetting machines are all retrofitted to be operated in zone 2 environments. High Pressure water jetting is highly effective and time-cost efficient method of cleaning that provides immaculate results. Hydro jetting can be used to provide a wide range of cleaning solutions such as the cleaning of heat exchanger tubes, coolers, Tanks, Process internals and pipelines. Our Hydro jetting machines can be fitted with a number of various accessories like Stoneage nozzles, Flexible Lance, Rigid Lance, and High Pressure Gun. All of our hydro jetters are qualified and highly experienced in the trade. Blasting water with Hydro jetting equipment at extremely high pressures is not without risks and hazards, but with our HSE procedures and protective equipment we manage to minimize the associated risks, guaranteeing a safe working environment for all.
Chemical/Foam Cleaning
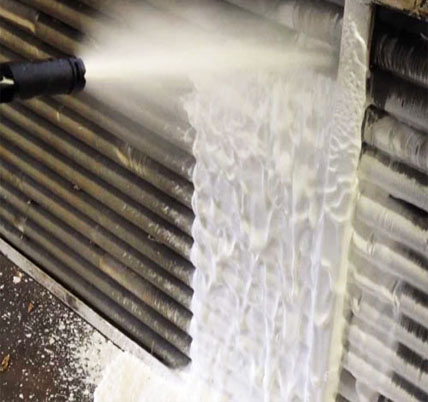
An effective and time-efficient solution, to removal fouling, with minimal access required to an exchanger's internals is chemical cleaning. Once a heat exchanger is identified to be chemically cleaned, Super Engineering Industry then studies the metallurgy and the nature and extent of fouling allowing its team of experienced engineers to determine the suitable chemical cleaning agent to be circulated.
Surface preparation
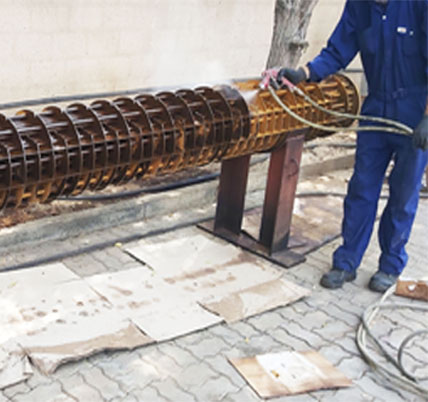
Man Power Supply Service

We are one of the reputed technical manpower supply company in UAE focused on providing manpower supply services throughout the Middle East for the past 10 years. We are the one-stop solution for manpower supply in UAE to the Shut down works and technical services requirements for all major industrial sectors such as Oil & gas sector, Energy industries, Desalination plants, process industries & others. Our goal is to provide quality manpower supply services to all our clients. Ensure your success with our expertise in manpower supply services.
Types of Heat Exchanger

- Shell and tube heat exchanger
- Plate heat exchangers
- Fin Fan Coolers
- Plate fin heat exchanger
- Parallel-flow heat exchanger
- Counter-flow heat exchanger
- Finned and Unfinned heat exchanger
- Fluid heat exchangers
- HVAC Air Coils
- Helical-coil heat exchangers
- spiral heat exchangers
- Evaporator & Economizer coils
- U Tube Bundles
- Floating & Fixed Heat Tube Bundles
Heat Exchanger Gallery
Material Grades
We deal in almost all hard to find material and we keep on exploring new supplier and sources to add our material portfolio

Major Heat Exchanger References
PROJECT | END-USER | SCOPE OF WORK | YEAR OF COMPLETION |
---|---|---|---|
ADNOC OFFSHORE PROJECT | ADNOC OFFSHORE | Refurbisment of T114 Reflex Condenser | 2021 |
Refurbishment of GT-3 Alternate Air Cooler DE-43600340 & NDE-43603045 | |||
Refurbishment of Alternate Air Cooler | |||
Refurbisment of T160-A Tube Bundle | |||
Refurbisment of T112 Tube Bundle | |||
Refurbisment of T103 Tube Bundle | |||
ADNOC GAS PROCESSING PROJECT | ADNOC GAS PROCESSING | Re-Tubing Of Instrument Air Compressor Fin Fan Cooler TAG NO: (15V101 – E1A/E2A/E3A) TAG NO.: (15V101 – E1A/E2A/E3A) | 2021 |
ADNOC REFINING PROJECT | ADNOC REFINING | Fabrication, Testing & Supply of Tube Bundle 803-E-010 A – 1 no. 803-E-010 B – 1 no. | 2021 |
Re-Tubing of U-Tube Bundle 1670-E-001C as per the Scope of Work | |||
ADNOC OFFSHORE PROJECT | ADNOC OFFSHORE | ZWSC GG2 PT Air T109 Coolers for refurbishment | 2020 |
USSC Bleed Air Cooler (7002 8163 shell & UTC 35819-Tube bundle) | |||
ZW GG2: T103 Refurbishment of Tube Bundle 43600149 | |||
GPF Instrument Aircompressor Final Stage Air Cooler | |||
ZWSC-GG2 Refurbishment of T104 Channel Head with Covers: 2 Sets | |||
Insitu Baseline Inspection & Maintenance of USSC ABK TIP | |||
G130 Alternate Cooler for refurbishment: 3 sets | |||
T101 New Upgraded Bundle Assembly | |||
CSP Sep #2 & Uap Synthetic Oil Eliminator Coolers Refurbishment & Replacement | |||
Repair of Partition Plate of US Heat Exchamgers at Das Island | |||
Refurbishment of PT Air Coolers with shell & Covers: 2 Sets | |||
Das Island - Boiler#8 tubes cleaning | |||
Fabrication & Supply GT2 Lube Oil Cooler Tube Bundle For Heat Exchanger - 2 Sets | |||
Design, Certification & Fabrication For Tube Bundle - T-103 Craddle (Lifting Basket) | |||
Aluminum Cooler Repair Welding | |||
Fabrication & Supply Fire Water Pumps - P 170 A/B/C/D/E - Lube Oil Cooler – 7 Nos Coil | |||
Fabrication & Supply Fire R-120 Motor Air Cooler For Heat Exchanger | |||
Fabrication & Supply Fire For Pt Air Cooler 6 Sets Shell, Tube Bundle & Cover (2 Set Horizontal & 4 Set Vertical) For Heat Exchanger | |||
Fabrication & Supply Fire Diesel Engine Jacket Water Cooler – 1 No | |||
Fabrication & Supply Fire Lifting Basket 3types – 6 Nos For Tube Bundle | |||
ADNOC OFFSHOREPROJECT | ADNOC OFFSHORE | Fabrication & Supply Of Power Turbine Air Cooler – 1 Nos | 2019 |
Assembling Of U Tube Bundle -1 Nos | |||
Fabrication & Supply Of Channel Head & End Cover | |||
Fabrication & Supply Channel Head & Cover – Heat Exchanger 2 Set | |||
Refurbishment Of Zcsc-Wip De Motor Cooler(HE) & Non De Motor Cooler(HE) – 2 SETS | |||
T-103 – Retubing U Tube Bundle For Heat Exchanger 23 Tons -1 Nos | |||
Dismantling, Refurbishment & Installation Exchangers & Radiators – 6 NOS | |||
Fabrication & Supply Of New T-115 Bundle – 2 Nos | |||
Fabrication & Supply Of New T-115 Shell & Cover- 2 Nos | |||
Fabrication & Supply Of New T-115 Complete Cooler Assy. -2 Nos | |||
Fabrication & Painting Shell (Spare) – 6 Nos | |||
Fabrication, External Painting, Internal Glass Flake Coating, Cuni Cladding On gasket Face Flangesof Channel Head & Cover For T-104 -2 Nos |
PROJECT | END-USER | SCOPE OF WORK | YEAR OF SUPPLY |
---|---|---|---|
New Upgraded Components for ZWSC –CGS Compressor | ADNOC GAS PROCESSING | Equipment : Tube Bundle Assembly for Recycle Coolers | 2020 |
ASME Sec VIII Div. 1 (U-stamp) + TEMA 9th Ed.Qty : 02 No | |||
TEMA Type: TEMA Class: R | |||
Design Press.(Shell side) : 21.6 Bar | |||
Design Press.(Tube side) : 10.35 Bar | |||
Design Temp. (Shell & Tube side): 150 /80 Deg C | |||
Corrosion Allowance: NIL | |||
Tube Material: SA 249 UNS 31257 | |||
Size 25.4 OD X 2.11 Thk (Min)-6096mm Length | |||
Stationary & Floating Tube sheet : SA 182 F44(UNS 31254)-68 mm Thk | |||
No. of Tubes: 548 (Each Quantity) | |||
FULCRUM SIERRA BIOFUELS PROJECT | ABENGOA | Equipment : Fixed Tubesheet Heat Exchanger of Economizer | 2019 |
ASME Sec VIII Div. 1 (U-stamp) + TEMA 9th Ed.Qty : 01 No | |||
TEMA Type: BXM (H); TEMA Class: R | |||
Design Press.(Shell side) : 42.7 Bar | |||
Design Press.(Tube side) : 42.7 Bar | |||
Design Temp. (Shell & Tube side): 232 Deg C | |||
Corrosion Allowance: NIL | |||
Shell Material: SA 240 TP 304 + NACE | |||
Concentric Reducer: SA 240 TP 304 +NACE | |||
Tube Material: SA 213 TP 304 | |||
Shell I.D : 500 mm | |||
Shell Thickness :18mm | |||
Tube Dia. 25.4mm x 1.651mm (Avg) x 800mm Long, | |||
No. of Tubes: 90 | |||
Hydro.Test Pressure (Shell & Tube Side) : 62 barg | |||
FULCRUM SIERRA BIOFUELS PROJECT | ABENGOA | Equipment : Kettle Reboiler ASME Sec VIII Div. 1 (U-stamp) + TEMA 9th Ed.Qty : 01 No | 2018 |
ASME Sec VIII Div. 1 (U-stamp) + TEMA 9th Ed.Qty : 01 No | |||
TEMA Type: BKU (H); TEMA Class: R | |||
Design Press.(Shell side) : 3.45 Bar | |||
Design Press.(Tube side) : 8 Bar | |||
Design Temp. (Shell Side): 177 Deg C | |||
Design Temp. (Tube Side): 204 Deg C | |||
Corrosion Allowance: NIL | |||
Shell Material: SA 240 TP 304 + NACE | |||
Tube Material: SA 213 TP 304 + NACE | |||
Shell I.D : 1475 mm | |||
Channel ID: 850 mm | |||
Shell & Channel Thickness :10mm | |||
Tube Dia. 19.05 x 1.651mm (Min.) x 6000mm Long,No. of ‘U’ Tubes: 424 | |||
Hydro.Test Pressure (Shell Side) : 4.23 barg | |||
Hydro.Test Pressure (Tube Side) : 11.4 barg | |||
UNCONVENTIONAL GAS DEVELOPMENT PROJECT | SAUDI ARAMCO | Equipment : Shell & Tube Heat ExchangersASME Sec VIII Div. 1 (U-stamp)+ TEMA 8th Ed.Qty : 01 No. | 2015 |
TEMA Type: BEM (H); TEMA Class: R | |||
Design Press.(Shell side) : 43.44 Bar | |||
Design Press.(Tube side) : 42.38 Bar | |||
Design Temp. (Shell Side): 210 Deg C | |||
Design Temp. (Tube Side): 210 Deg C | |||
Shell (Pipe) Material : SA 106 Gr.B + NACE | |||
Shell Outer Dia : 508 mm | |||
Thickness :15.09mm | |||
Hydro.Test Pressure (Shell Side) : 56.54 barg | |||
Hydro.Test Pressure (Tube Side) : 56.74 barg | |||
BP SHAH DEN | BP(Oil industry company) | Equipment : Shell & Tube Heat Exchangers of Well Effluents Heater | 2015 |
ASME Sec VIII Div. 1 (U-stamp) + TEMA 9th Ed + API 660 8th Ed.. | |||
Qty : 01 NoTEMA Type: DET (V); TEMA Class: R | |||
Design Press.(Shell side) : 16.2 Bar | |||
Design Press.(Tube side) : 130 Bar | |||
Design Temp. (Shell Side): 200 Deg C C | |||
Design Temp. (Tube Side): 200 Deg C | |||
Corrosion Allowance: 3mm on shell side / NIL on Tube side | |||
Shell Material: SA 2516 Gr.70 | |||
Tube Material: SA 213 TP 321 | |||
Shell I.D : 735 mm | |||
Channel ID: 549 mm | |||
Shell / Channel Thickness :10mm / 32+3mm Thk., | |||
Tube Dia. 38.1 x 4mm (Min.) x 4572 mm Long,No. of Tubes: 72 | |||
Hydro.Test Pressure (Shell Side) : 24.3 barg | |||
Hydro.Test Pressure (Tube Side) : 222 barg | |||
ZWSC-GGII | ADMA-OPCO | Equipment : Glycol Re-boiler Shell with SDSS material | 2015 |
Replacement of existing shell with nozzles and internal supports | |||
Qty : 01 Nos | |||
Shell Material : UNS 32750 (Super Duplex) | |||
Dia: 900mm | |||
Thickness: 8mm | |||
Tan. To Shell Flange Face : 5600 mm | |||
IGD PROJECT OFFSHORE FACILITIES | ADMA-OPCO | Repair work of heat Exchange( Inlet Gas Coolers ) | 2015 |
Quantity : 2 Nos | |||
Carry out the repair work, ie pre machining, weld build-up and machining to reinstate the original shape, size and surface finish as per | |||
the Repair recommendations and as stated below: | |||
The flange gasket seating cladded areas shall be machine upto 4.5 mm. | |||
-Visual check shall be carried out. | |||
-If any further pittings noted, the same shall be ground off. | |||
-The parent metal pitting removal areas shall be welded with p1 | |||
welding consumables. | |||
-Then the cladding shall be welded up to 7-8 mm. | |||
- Machining shall be done to achieve 4.5 mm. | |||
- PT shall be done on the cladded machined surface | |||
-Eddy current Test of all U-Tubes |